What is
destructive testing ?
Destructive testing is a type of test used in manufacturing that ultimately destroys the sample under test. Used to determine the strength, safety and life of products, destructive testing is often used to test welds, but is probably best known as a method of testing the safety of cars. Destructive testing comes in three forms: stress or stability; impact or safety; and hardness or strength testing.
Welds, in particular, are subject to many types of destructive testing when used on products. Welds undergo stress, impact and hardness testing. Free bend, break line cut, etch and fillet weld tests are all types of stress tests that test the strength and quality of a weld. Impact tests are designed to break the weld in a single blow from different angles. Welds are also subjected to tensile strength tests, which pull the weld at both ends until it separates. Recording under what conditions the weld breaks gives researchers important information about the use of this type of weld and the conditions that can make the weld unsafe.
The international standards specify the dimensions of the specimens and the procedures to be used in texture testing to obtain information on the types, dimensions and distribution of internal defects, such as blowholes, cracks, sticking, lack of penetration and solid inclusions, on the fracture surface.
For welds they apply to all forms of products made of metallic materials with a thickness of 2 mm or more, joined by any fusion welding process.
Eurocontrol carries out destructive tests for the characterisation of materials, welding procedures, etc...
Our services


This work is combined with other lines of action such as the qualification of welding procedures and welders or the study of chemical composition. Among the operations we carry out, the following can be found:
- Tests for the qualification of welding processes and welders, which include traction, bending, hardness, toughness studies, microscopic and macroscopic studies.
- Tests for the characterisation of materials, mechanical resistance, elastic limit, hardness, resilience.
- Chemical analysis with spark, arc and/or X-ray equipment. This equipment is portable and can be used in the workshop, although if greater precision is required, laboratory equipment can be used.
- Tests for the qualification of painting processes, such as adhesion tests, salt spray tests, etc...
- Other tests that we can carry out depending on the customer's needs, such as corrosion studies, fatigue, fracture toughness, etc...
Discover our other
related services
Why choose Eurocontrol?
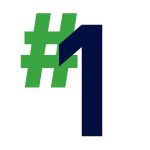
a team of experts at your disposal
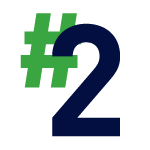
Geographical coverage nationwide
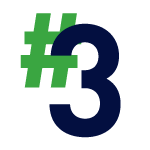